Confused about whether you need a muffle furnace or a lab oven? Choosing the wrong one can waste time, ruin samples, and cost you money.
The main difference lies in temperature range and application. Muffle furnaces reach much higher temperatures (often over 1000°C) for processes like ashing or heat treating, while lab ovens typically operate below 300°C, primarily for drying, sterilizing, or moderate heating.
As someone who's been manufacturing and exporting lab equipment from China for over 16 years with ZZKD, I've seen this confusion countless times. It's easy to think they're similar – both heat things up, right? But understanding their distinct purposes is crucial for getting your lab work done efficiently and accurately. Let’s break down what sets them apart, starting with some specific types you might encounter.
What Makes a Carbolite Muffle Furnace Special?
Need extremely reliable, high-temperature heating but worried about inconsistent results or equipment failure? Finding a trustworthy furnace can be a challenge.
Carbolite Gero is a well-known brand recognized for manufacturing high-quality, durable muffle furnaces with precise temperature control and features often tailored for specific, demanding applications in research and industry, though typically at a premium price point.
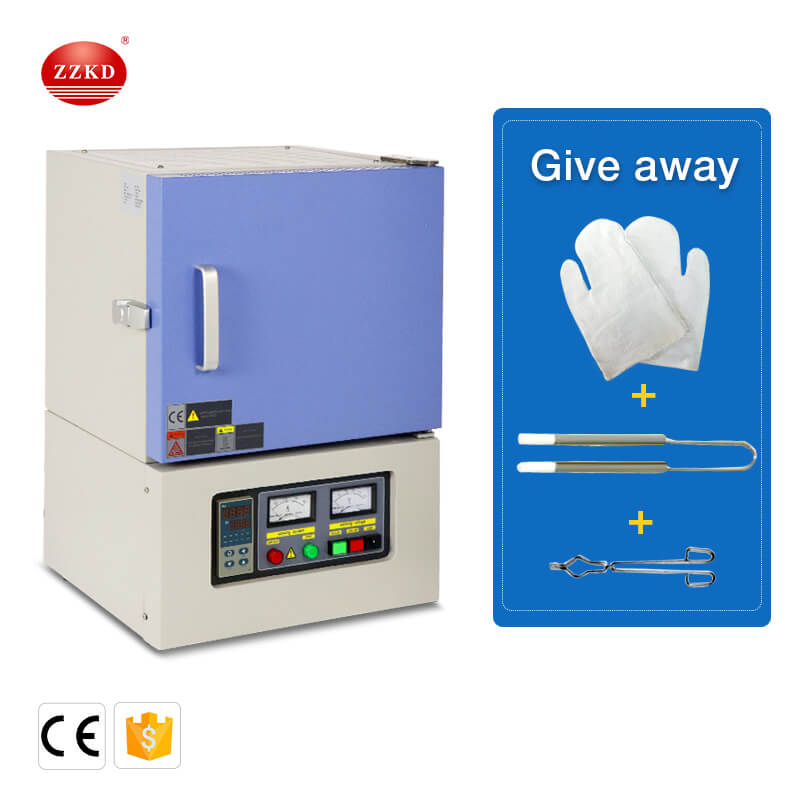
When we talk about brands like Carbolite, we're often discussing equipment known for its specific engineering standards, materials, and potentially advanced features. While we at ZZKD pride ourselves on producing robust, reliable, and cost-effective muffle furnaces designed for the international market, understanding what makes premium brands stand out helps clarify furnace features overall. Generally, high-end furnaces might offer things like:
Key Features Often Associated with Premium Brands:
-
Superior Temperature Uniformity: Advanced insulation and element placement ensure the temperature is consistent throughout the entire chamber, crucial for sensitive processes.
-
Advanced Controllers: Multi-segment programming, data logging capabilities, digital communications (like Ethernet), and enhanced safety features (over-temperature protection).
-
Specialized Atmospheres: Options for introducing inert gases (like nitrogen or argon) to prevent oxidation during heating.
-
Construction Materials: Use of high-grade alloys, specific refractory materials, and robust casings designed for longevity under harsh conditions.
-
Certifications & Standards Compliance: Often designed and certified to meet specific international safety and performance standards required by certain industries.
From my experience dealing with customers worldwide, the need often boils down to balancing performance, reliability, and budget. While a premium brand offers certain assurances, we focus on providing excellent value, ensuring our electrical muffle furnaces meet rigorous quality checks (like ISO and CE certification) and deliver the high temperatures and control needed for most standard laboratory applications effectively.
How Does an Electrical Muffle Furnace Actually Work?
Unsure about the inner workings of an electrical muffle furnace? Understanding the basics helps in operation, troubleshooting, and appreciating its capabilities.
An electrical muffle furnace works by passing electricity through high-resistance heating elements surrounding an insulated chamber. These elements heat up significantly, transferring radiant heat to the chamber and the sample inside, achieving high temperatures without direct flame contact.
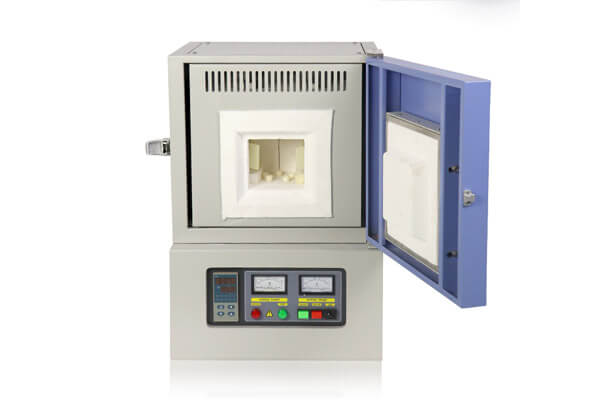
Let's get a bit more technical, based on the furnaces we build right here in Zhengzhou. The core principle is simple resistance heating, similar to an electric stove element but engineered for much higher temperatures and contained within a highly insulated box. Here’s a breakdown of the key parts:
Core Components:
-
Heating Elements: These are the heart of the furnace. Common types include Kanthal (iron-chromium-aluminum alloy) wire for temperatures up to ~1300°C, Silicon Carbide (SiC) rods for up to ~1600°C, and Molybdenum Disilicide (MoSi2) elements for even higher temperatures (up to 1800°C or more). The choice depends on the required maximum temperature and budget.
-
Insulation Chamber (Muffle): This is the inner chamber holding the sample. It's typically made from high-purity ceramic fiberboard or refractory bricks. This material must withstand extreme heat, prevent heat loss, and avoid reacting with the samples. The insulation is critical for efficiency and maintaining uniform temperature.
-
Temperature Controller: This is the brain. It uses input from a thermocouple (a sensor measuring temperature) placed inside the chamber to regulate the power sent to the heating elements, ensuring the set temperature is reached and maintained accurately. Modern controllers are usually PID (Proportional-Integral-Derivative) based for precision.
-
Thermocouple: A sensor, often Type K, S, or B, depending on the temperature range, that measures the internal temperature and sends a signal to the controller.
-
Outer Casing: A metal shell (usually steel) that houses all the components and provides structural support. It often includes vents for cooling electronics and releasing any fumes (a proper exhaust system is usually needed separately).
The beauty of electrical heating is its cleanliness (no combustion byproducts) and controllability. When we design our furnaces, we carefully select element types, insulation thickness, and controller configurations to match the performance needs of labs and industries globally, ensuring reliable heating cycle after cycle. We also focus on safety features like door switches that cut power when opened.
What Are Common Uses for a Laboratory Muffle Furnace?
Got a high-temperature task in the lab but not sure if a muffle furnace is the right tool? Knowing its typical applications helps match the equipment to the job.
Laboratory muffle furnaces are primarily used for high-temperature applications such as determining the inorganic ash content of samples (ashing), heat-treating small metal parts (annealing, hardening), materials testing (like firing ceramics), and quantitative gravimetric analysis requiring ignition.
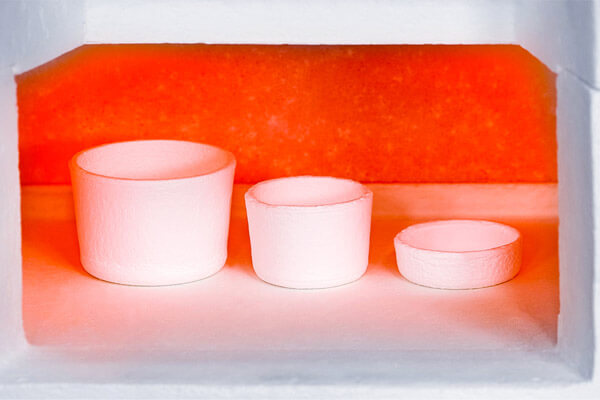
Having supplied our ZZKD muffle furnaces to labs across 87 countries, we've seen them used in a huge variety of settings – from university research departments to industrial quality control labs. Their ability to reach and hold high temperatures accurately makes them indispensable for specific tasks that ovens just can't handle. Let's look deeper:
Key Laboratory Applications:
-
Ashing / Loss on Ignition (LOI): This is perhaps the most common use. Samples (like food, coal, plastics, waste materials) are heated at high temperatures (e.g., 550°C, 900°C) to burn off all organic matter, leaving only the inorganic ash. Weighing before and after gives the ash content or LOI, crucial for quality control and analysis.
-
Heat Treatment of Materials: Small metal components can be annealed (softened), hardened, or tempered. Ceramics can be sintered or fired. Glass can be fused or treated. Researchers use them to test material properties after exposure to extreme heat.
-
Gravimetric Analysis: Certain chemical analysis procedures require a precipitate to be heated to a constant weight at high temperatures before final weighing.
-
Materials Science Research: Developing and testing new materials often involves subjecting them to controlled high-temperature cycles.
-
Quality Control: Industries use muffle furnaces to test the heat resistance of components or coatings, or to perform standard test methods requiring high heat (e.g., asphalt binder content).
Safety Considerations:
Working with such high temperatures demands caution. Proper ventilation is essential to remove fumes. Heat-resistant gloves and tongs are necessary for handling crucibles. Users must be aware of the thermal inertia – the furnace stays dangerously hot long after being switched off.
Understanding these uses helps our customers – whether they're in pharmaceuticals, environmental testing, or academia – select the right size and temperature range for their muffle furnace needs. It ensures they get a tool perfectly suited for their high-temperature work.
Conclusion
Essentially, choose an oven for lower-temp drying/heating (below 300°C) and a muffle furnace for high-temp work (above 500°C) like ashing or material treatment. We're here to help you choose wisely!