Finding a reliable chemical reactor is tough. You worry about performance failures, project delays, and poor communication with suppliers, which can ruin your research and production schedules.
To choose the right chemical reactor manufacturer, focus on companies with over 16 years of direct export experience and essential certifications like ISO9001 and CE. Prioritize manufacturers who offer customization, transparent communication with English-speaking engineers, and a proven global track record for reliability and performance.
Selecting the right partner for your lab equipment is a critical decision. It’s not just about buying a piece of machinery; it’s about investing in a tool that will be at the heart of your work for years to come. Over my 16 years in this industry, I've seen firsthand how the right equipment can accelerate discovery. A good manufacturer isn't just a seller; they are a partner in your success. They understand the challenges you face and provide solutions, not just products. This foundation of trust and reliability is what you should look for.
What Makes a Glass Reactor from a Top Manufacturer Different?
You see glass reactors everywhere, but they are not all the same. A cheap one might look good online, but it could crack under thermal stress or leak, jeopardizing your entire experiment.
A top-tier jacketed glass reactor stands out due to its high-borosilicate 3.3 glass, ensuring superior thermal shock resistance and chemical stability. Leading manufacturers like us provide precise temperature control, robust stirring systems, and a verified leak-free design, all backed by CE and ISO certifications for safety.
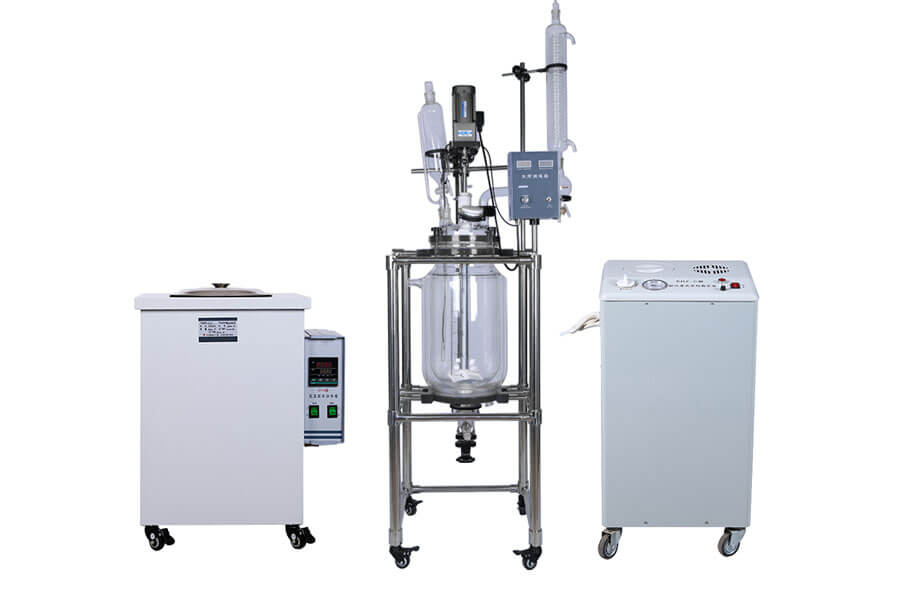
When you really look at what separates a standard glass reactor from a professional-grade one, the details become very important. It’s not just about the glass itself, but how the entire system is built and supported. We focus on these details because we know they make a huge difference in your daily work. From the seals to the support frame, every component is chosen for durability and performance. This is why we can confidently say our reactors are built for serious research and production.
Material Quality is Key
The foundation of any great glass reactor is the glass. We exclusively use high-borosilicate 3.3 glass. This isn't just any glass; it’s a specific type known for its excellent thermal properties. It can handle rapid temperature changes without cracking, a common issue with lower-quality glass. It’s also highly resistant to chemical corrosion, which means you can work with a wide range of materials without worrying about damaging the reactor or contaminating your experiment. We ensure our glass has uniform thickness, which is critical for even heat distribution and mechanical strength.
Engineering for Precision and Safety
A reactor is more than just a glass vessel. The engineering behind it defines its performance. We design our stirring systems to create a perfect vortex for mixing, with adjustable speeds to match your process. The sealing is another critical area. We use PTFE seals combined with precision-engineered components to ensure a deep vacuum can be held without any leaks. This is vital for processes that are sensitive to air. Furthermore, the support frame is made of stainless steel, providing a sturdy, stable, and corrosion-resistant base for the entire setup, ensuring safety and longevity in a busy lab environment.
Why is a High-Pressure Reactor a Specialized Purchase?
Working with high-pressure reactions is inherently risky. You can't just use any vessel; you need equipment that is specifically designed and certified to handle the intense conditions safely and reliably.
A high-pressure reactor is a specialized purchase because it must guarantee safety under extreme conditions. We manufacture ours from robust materials like SS316L or Hastelloy, featuring reinforced designs, and critical safety mechanisms like rupture discs and pressure-relief valves, all certified to international standards.
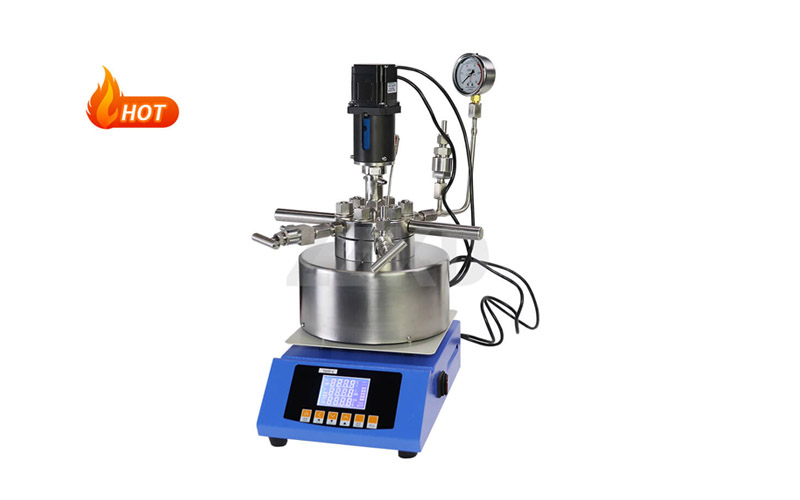
When I talk to customers about high-pressure reactors, the first word I always use is "safety." These are not standard pieces of equipment. They are designed for some of the most demanding chemical processes. The trust you place in a high pressure reactor manufacturer is immense, and we take that responsibility seriously. Every weld, every seal, and every valve is a safety-critical component. This is why our experience matters. We've spent over 16 years perfecting our designs and manufacturing processes to ensure that when you use our equipment, you can focus on your chemistry, not on worrying about the hardware.
Choosing the Right Material
The choice of material is the most critical factor for a high-pressure reactor. The material must withstand both high pressure and chemical attack from the reactants. We help our customers choose the right material for their specific application.
Material |
Key Features |
Common Applications |
Stainless Steel (SS316L) |
Good corrosion resistance, strong, cost-effective. |
General chemical synthesis, polymerizations, hydrogenation. |
Hastelloy (C-276) |
Excellent resistance to strong acids and chlorides. |
Processes with highly corrosive chemicals, pharmaceuticals. |
Titanium |
Very high strength-to-weight ratio, superb corrosion resistance. |
Saltwater applications, reactions with oxidizing acids. |
Essential Safety Features
You cannot compromise on safety. Our high-pressure reactors include multiple layers of safety features. A rupture disc is a primary safety device designed to burst at a pre-set pressure to prevent catastrophic failure. We also include a pressure relief valve as a secondary measure. Our magnetic stirring coupling is another key safety feature. It allows for powerful stirring inside the sealed vessel without a physical shaft penetrating the reactor head, which eliminates a potential leak path for hazardous materials under pressure. These features are not optional; they are essential for safe operation.
Conclusion
Choosing the right chemical reactor manufacturer means finding a partner with experience, quality materials, and a commitment to your success. We are here to be that partner for you.