As a very important reactor in chemical technology, the reactor plays a very important role in chemical production. It is also one of our main products. It is divided into glass reactor and stainless steel reactor.Among them, the material of the glass reactor is Borosilicate glass. According to the capacity, it can be divided into:
2L jacketed glass reactor, 10l jacketed glass reactor, 20L jacketed glass reactor, 50l jacketed glass reactor, 100l jacketed glass reactor and so on.
The control of the temperature in the reactor is very critical. It involves not only the efficiency of the chemical reaction, but also the quality of the product. At the same time, the stable operation of the device is of great significance to the safety of life and the emission of polluting gases.
Structural composition and working environment of the chemical glass reactor
glass reactor is one of the typical equipment commonly used in the chemical, pharmaceutical and food industries. From the perspective of composition structure, the reactor is mainly composed of a kettle cover, a jacket, a kettle bottom, and a stirrer.Generally speaking, if the stirring device is relatively large in height and diameter, multiple stirring blades can be used to stir more materials evenly.The laboratory glass reactor mainly uses steam, hot oil and other media to increase the temperature in the reactor through heat exchange.In the glass double jacket reactor, the main temperature control is to control the loop through the adjustable valve on the conductive medium pipeline of the reactor through thermal resistance and thermocouple, etc., so as to control and adjust the temperature.Outside the wall, a jacket device is usually provided, or a heat exchange surface is set inside the container, and then heat energy is exchanged through an external circulation.
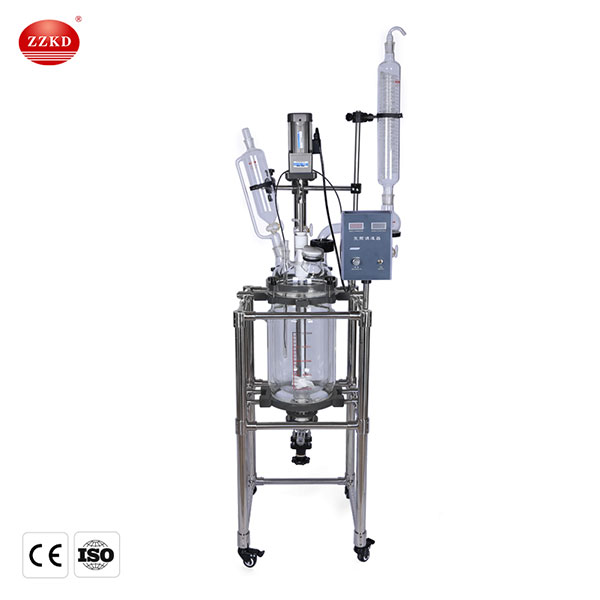
The inside of the chemical laboratory glass reactor usually requires a relatively large operating pressure, and the internal pressure in the glass laboratory reactors is usually formed by the high temperature during the reaction.In the glass double jacket reactor, sometimes the pressure fluctuates greatly, or the operation of the staff makes the working environment unstable. At this time, the temperature in the reactor will suddenly rise relatively quickly, so sealing means must be adopted in the reactor.If it is a relatively low pressure environment, the filler is used for filling, and the pressure used is generally relatively low. Under medium pressure conditions, medium pressure or mechanical means will be used for filling, and the negative pressure is generally 4kg.If it is under high pressure, magnetic sealing is performed. Generally, such sealing means can reach a pressure of 14kg. In the use of magnetic seals, cold water is generally used for cooling.For other sealing methods, if the temperature in the chemical laboratory glass reactor exceeds 120°C, use cold water to add a cold water jacket for cooling.Due to the higher sealing performance and higher operating pressure in the reactor, higher materials are required for production.The material in the reactor is generally carbon-manganese steel, stainless steel, zirconium and other metals or alloys, or Borosilicate glass.
Reaction principle in laboratory glass reactor
In the chemical laboratory glass reactor device, the inside of the reactor can usually use molten coal for stirring reaction, and the interlayer usually uses refrigerant or hot oil for cooling or circulating heating. Other materials can also be injected to heat or cool the reaction at a constant temperature. This will help the reaction proceed smoothly.At the same time, the materials also need to be reacted under appropriate pressure conditions, usually under negative pressure or normal pressure for stirring reactions.The reaction materials are carried out in the reaction kettle, and the reaction progress is controlled by controlling the evaporation and reflux of the reaction solution. The materials can usually be discharged through the bottom outlet of the reaction kettle.